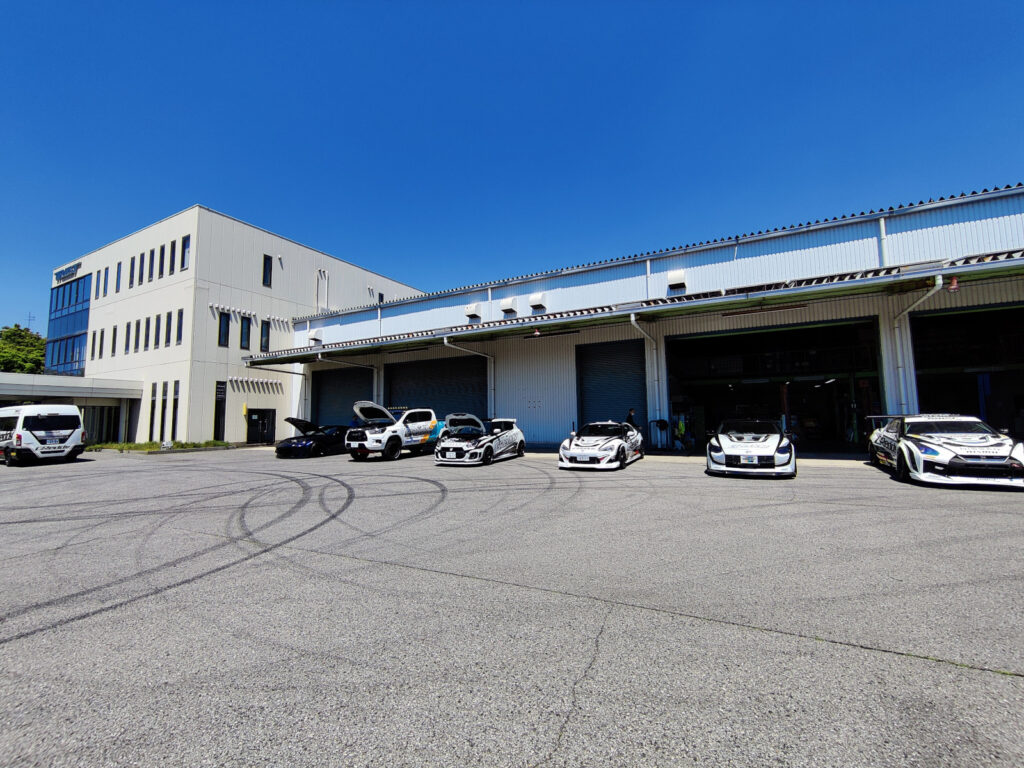
During a recent visit to the Japanese parent company Trust (manufacturer and owner of the GReddy brand) in the suburbs of Tokyo, Japan, we were able to discover their front lips production workshop.
It all starts with the preparation of the chemical compound used to make the lips: a black resin, mainly based on ethyl carbamate, better known as urethane.
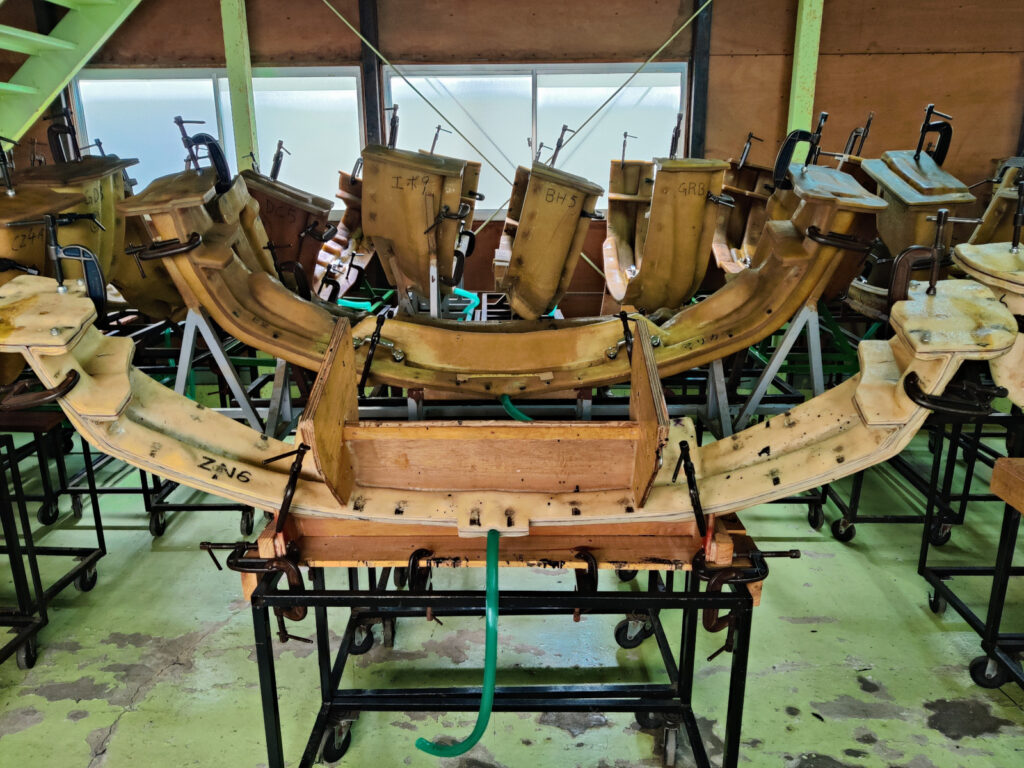
The operator then carefully prepares the necessary moulds according to his order book, and closes them as tightly as possible using bolts and clamps. The liquid urethane is injected under pressure through the green hoses in the centre of each mould. Can you identify all the models in the photos?
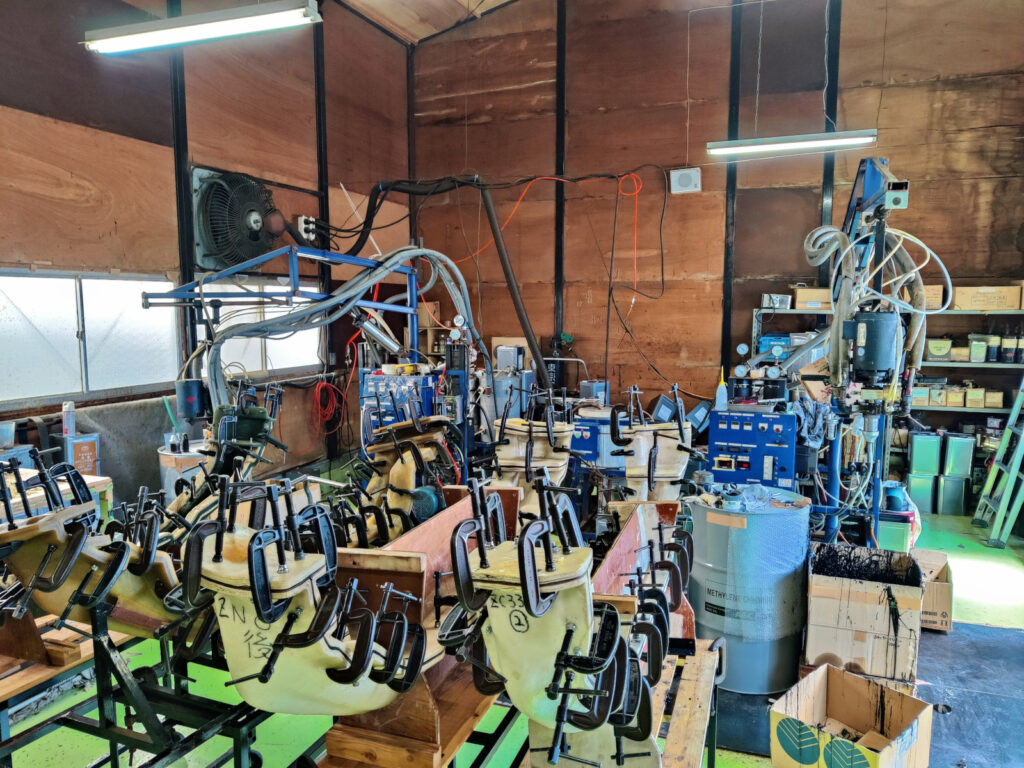
After a drying and curing period lasting several hours, the lips are carefully removed from the moulds and inspected with a magical Japanese rigour. In other words, the manufacturing process is completely handmade, but achieves a perfectly industrial level of quality.
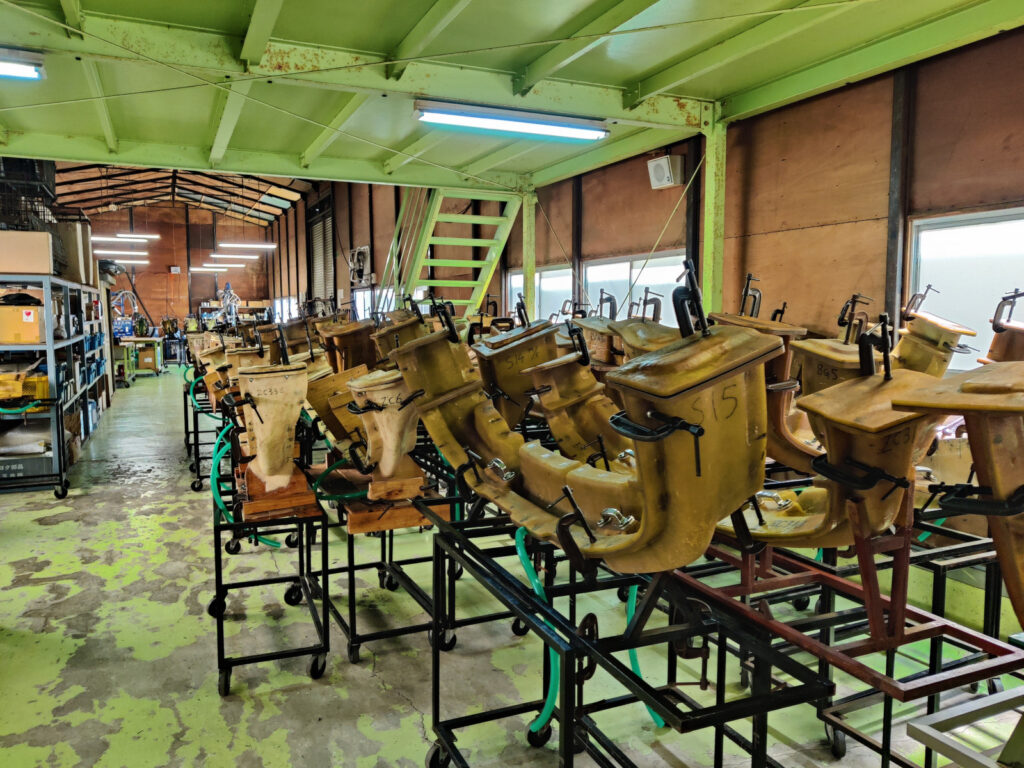
The finishing stages (deburring, sandblasting, polishing, cleaning the moulds) are carried out entirely by hand, for a perfect visual appearance and assembly fit. Each lip is a one-off, yet if you compare several made years apart, it’s impossible to detect the slightest difference.
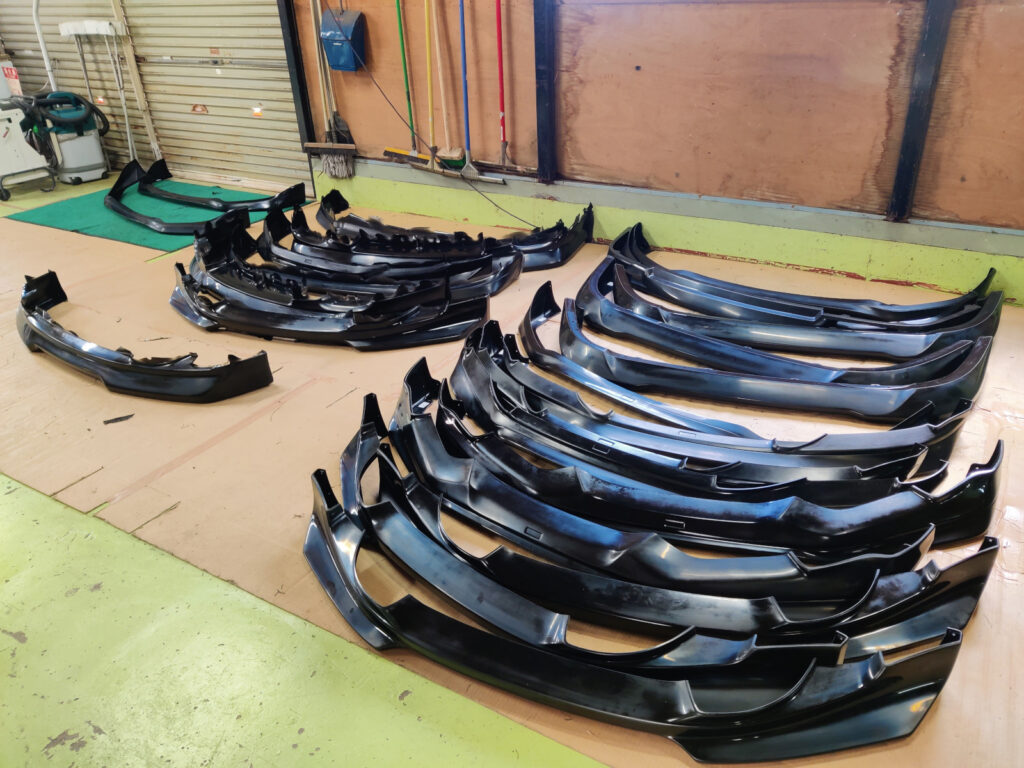
At GReddy, there are no assembly lines or minimum quantities. Operators produce only the quantities ordered by DriftShop, following the ‘kanban’ production method, historically devised by Toyota and which can be summed up as follows: “produce only what is needed, at the exact time it is needed”.